Established in 1863, the Riverside Precinct at St Mary’s College Ipswich has undergone a $9.8 million development, that was part of an overall redevelopment of the college grounds and facilities.
Used in this project
- Products
- LYSAGHT LONGLINE 305®
- Materials
- COLORBOND® steel - Classic finish
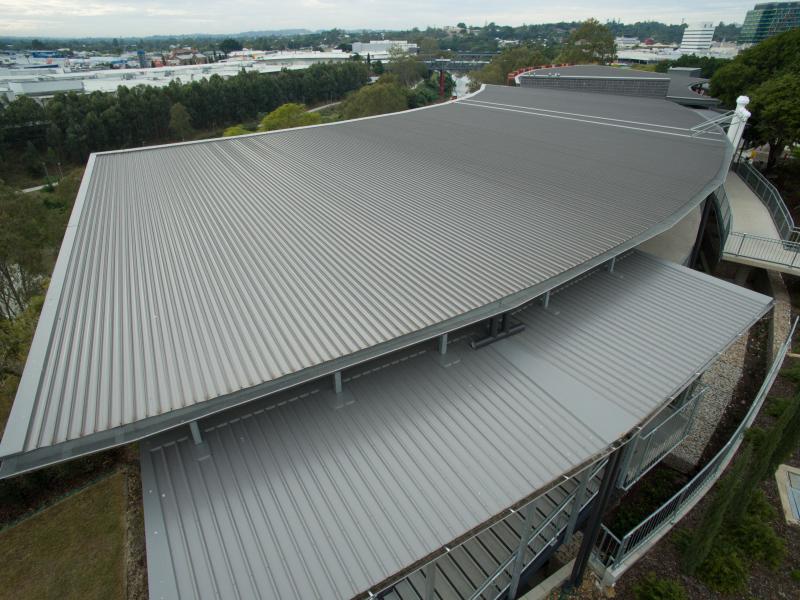
THE PROJECT
The $9.8 million development of the Riverside Precinct at St Mary’s College Ipswich is part of an overall redevelopment of the college grounds and facilities.
The college was established in 1863 by the Catholic Sisters of Mercy and is part of the Ipswich Heritage Trail. An important icon for the local community it is a prominent landmark for the city.
The new Riverside Precinct replaces a string of demountable buildings that were previously situated on the college’s “prime real estate” on a rise overlooking the Bremer River.
The project involves a number of inter-connecting buildings exhibiting a curvelinear shape to follow the contours of the site.
The finished buildings house 17 teaching spaces including Art, Science, Home Economics, Hospitality and Music, Dance, Drama.
THE SOLUTION
The radial design of the buildings’ roof area presented an ideal opportunity to showcase the unique tapering capability of LYSAGHT LONGLINE 305® cladding.
With its wide, flat pans and bold vertical ribs LONGLINE 305® cladding provides a strong, linear visual statement to the roof line of these building. Utilising tapered sheets of the long length, concealed fix decking enabled the contractor to achieve a continuous watertight finish which embraced the unique radial design of the structure.
THE PROCESS
The Riverside Precinct project was constructed during early 2015 and was completed in time for 3rd Term classes to begin in June.
Long length 16 metre sheets of LONGLINE 305® steel were manufactured at the Lysaght Emu Plains facility in western Sydney and road freighted to Ipswich on special long-load trailers. Consecutive sheets were manufactured, bundled and delivered to site on a JIT basis to minimise site congestion and maximise on-site efficiencies.
The complex ‘Double S’ curve design potentially presented significant issues with alignment of the individually tapered sheets to ensure that each sheet was perfectly installed in its correct position. To assist the roofing contractor Lysaght developed an innovative ‘laying grid’ that showed the exact location of where every individual sheet needed to be.